1 中国铝塑膜行业市场综述
1.1铝塑膜的定义与分类
铝塑膜是软包锂电池电芯封装的关键材料,单片电池组装后用铝塑膜密封形成电池,可以起到保护电池内部电芯材料的作用。铝塑膜由外阻层(ON层)、阻透层(AL层)、热封层(CPP层)通过胶黏剂复合而成,外阻层由尼龙构成,位于最外侧,用来保护铝箔免于划伤,减少碰撞对电池带来的伤害。阻透层由压铝箔构成,位于中间层,起到防止氧气、水分侵入的作用。热封层由流延聚丙烯膜组成,位于最内侧,起封口粘接的作用。铝塑膜在阻隔性、冷冲压成型性、耐穿刺性、化学稳定性和绝缘性方面有严格要求,是锂电池产业链中技术难度最高的环节,对软包锂电池的质量有至关重要的影响。
铝塑膜常见的分类方式是按照生产工艺的不同进行划分,在这一分类标准下,铝塑膜可分为干法铝塑膜和热法铝塑膜。干法以日本昭和电工(以下简称“日本昭和电工株式会社”)生产工艺为代表,在制备过程中用胶黏剂将AL层和CPP层粘接,再直接压合而成。热法以日本大日本印刷公司(以下简称“大日本印刷”)生产工艺为代表,先用MPP将AL层和CPP层粘接,再缓慢升温升压热合成制备铝塑膜。干法工艺对生产设备要求不高,但工艺流程较复杂,操作难度大。热法工艺对设备要求高,工艺流程简单,生产效率高,不需要废气的处理设施。相对于湿法工艺铝塑膜而言,干法工艺铝塑膜应用更加广泛,适用于大倍率、高能量的动力电池,是目前市场上主流铝塑膜厂商普遍采用的生产工艺方式。
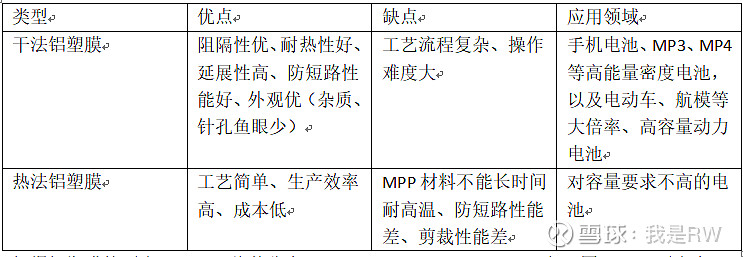
根据铝塑膜的厚度不同,将其分为88μm、113μm、152μm三种,厚度为88μm和113μm的铝塑膜适用领域为消费类电子产品,其中厚度为88μm的铝塑膜适用于薄型化数码电池,厚度为113μm的铝塑膜适用于3C移动电池。而厚度为152μm的铝塑膜适用于动力电池领域,如新能源汽车动力电池和工业储能动力电池等,对生产工艺的要求更高,价格更贵。
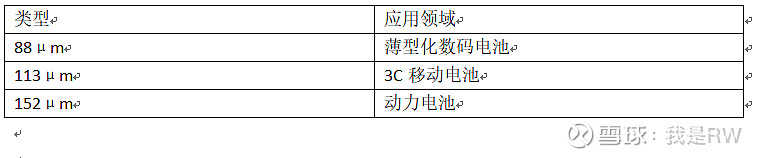
另外,根据铝塑膜下游应用领域的不同,可将其分为3C消费电子铝塑膜、动力软包铝
塑膜、储能铝塑膜和其他类铝塑膜:
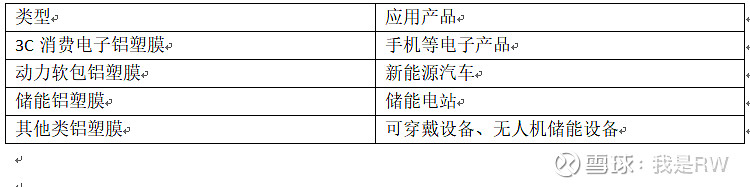
1.2 中国铝塑膜行业发展历程
铝塑膜最早由日本昭和电工开发生产,大日本印刷将其推广发展壮大。作为软包锂电池的关键封装材料,铝塑膜是锂电池产业链中技术壁垒最高的环节,对原材料、生产技术、设备工艺都有较高要求。由于技术难度高,中国铝塑膜行业长期被日本企业垄断,进口铝塑膜产品价格较高导致国内下游电池厂商成本较大,进口替代空间广阔。从2004年开始,中国部分企业开始布局铝塑膜产品,逐渐开启了铝塑膜国产化的新篇章。中国铝塑膜行业经历了进口依赖、探索研发和初步发展三个阶段。
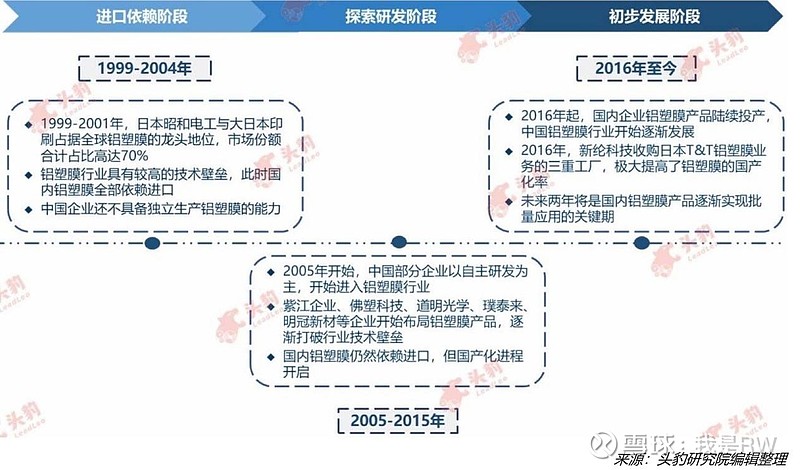
(1)进口依赖阶段(1999-2004年)
1999年,日本昭和电工与日本索尼公司共同研发生产出第一代铝塑膜产品,2001年继续推出第二代铝塑膜产品。同年,大日本印刷开始自主研发铝塑膜产品,日本昭和电工和大日本印刷打开了全球铝塑膜的市场空间。由于铝塑膜行业具有较高的技术壁垒,中国企业还不具备独立生产铝塑膜的能力,中国电池厂商所需铝塑膜全部依赖进口。
(2)探索研发阶段(2005-2015年)
为了封锁技术,日本、韩国等铝塑膜企业很少在中国建设生产基地,导致国外企业在售后服务和不良率处理方面存在滞后性,当国内下游电池厂商进口的铝塑膜出现质量问题时,无法快速对产品进行改善,损害国内电池厂商的利益。同时,国内铝塑膜完全依赖进口,进口铝塑膜产品价格比国产铝塑膜产品高,削弱了国内下游电池厂商的议价能力,电池原材料成本高,给电池厂商造成了显著的成本压力。
昂贵的产品价格和滞后的售后服务驱使下游电池厂商提高对自主研发生产的铝塑膜的诉求,进口替代的需求愈发强烈。在中国铝塑膜行业具有较大的成长空间和较高的盈利水平背景下,2005年起,中国部分企业以自主研发为主,开始进入铝塑膜行业,于此中国铝塑膜行业初具萌芽。
(3)初步发展阶段(2016年至今)
在国内企业不断提升自主研发工艺的背景下,2016年起,国产铝塑膜在质量和性能上逐渐达到了部分国内下游电池厂商的要求,虽然国内市场仍被日本昭和电工和大日本印刷等公司所垄断,但随着国内企业铝塑膜产品陆续投产,中国铝塑膜行业规模逐步扩张,国产化进程也在不断提速。
近年来,国产铝塑膜在设备、技术工业、材料等方面都在持续更新和完善,产品一致性、质量和耐电解液性能都取得了较大发展。目前国内企业的铝塑膜产品已经广泛应用于中低端3C消费锂电池领域,并逐渐向高端市场渗透,实现了从2015年国产化率为0到2020年国产化率约为10%的跨越。但现阶段,在储能领域及新能源汽车领域,铝塑膜技术和产品依旧处于被日本企业垄断的状态,其核心技术依旧掌握在日本企业手中。同时,全球约90%的市场份额被大日本印刷株式会社、日本昭和电工、日本凸版因数株式会社和韩国栗村化学占据,其中,前两者占据了全球市场的70%。
目前,从日本进口的铝塑膜在国内的市场份额超过90%,自主研发生产的铝塑膜市场竞争力较弱。随着国内生产技术水平的不断提高,在国家政策的驱动下,中国铝塑膜行业的国产化进程将逐步加快,未来两年将是国内铝塑膜产品逐渐实现批量应用的关键期。
1.3 中国铝塑膜行业市场规模
铝塑膜是软包锂电池的关键封装材料,其市场规模的增长主要受益于软包锂电池的发展,软包锂电池在安全性、能量密度、循环寿命等方面较方形锂电池和圆柱锂电池具有一定的优势,在3C消费电子领域、动力领域和储能领域应用广泛。近年来锂电池行业整体发展迅速,带动软包锂电池的市场需求持续增长,同时软包锂电池凭借其优秀的性能,在锂电池市场中的渗透率逐渐提高,软包锂电池行业的景气发展带动铝塑膜市场规模不断扩大。数据显示,中国铝塑膜市场规模从 2012 年的 11.5 亿元增加到 2019 年的 50.1 亿元。未来五年,得益于新能源汽车的快速发展,软包锂电池在动力领域的市场空间将逐渐扩大,中国铝塑膜行业市场规模将随之扩大。
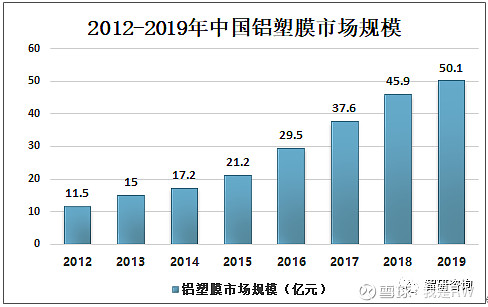
受如下三方面原因驱动,中国铝塑膜行业市场规模将持续增长:
(1)行业盈利空间大,进入壁垒逐渐降低,推动企业布局铝塑膜产品,提升企业实力
并带动行业不断发展。
(2)国产替代需求日渐强烈,市场空间广阔,促进行业国产化进程加快。
(3)下游软包电池发展潜力巨大,下游市场整体需求强劲,推动行业整体发展。
1.4 中国铝塑膜行业的产业链分析
中国铝塑膜行业产业链分为三部分:产业链上游参与者为尼龙、压延铝箔、CPP、胶黏剂等原材料供应商,产业链中游环节主体为铝塑膜生产企业,产业链下游是软包锂电池生产企业,其终端对应领域为3C消费电子、新能源汽车、电动工具及储能电站等。
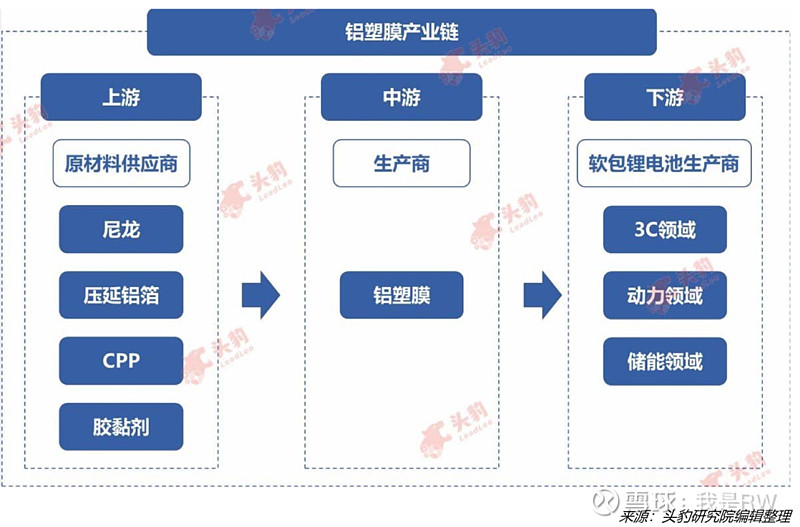
1.4.1 上游分析
铝塑膜行业产业链上游参与者为尼龙、压延铝箔、CPP、胶黏剂等原材料供应商。压延铝箔成本占铝塑膜产品售价的35%,占比最高。其次是CPP,占比 15%。占比第三的为尼龙,为 6%。最后是胶黏剂,占比3.5%。原材料成本约占铝塑膜售价的60%,大部分中游铝塑生产厂商原材料依赖进口,大大削弱了铝塑膜厂商的盈利能力。原材料生产技术要求高,成为制约铝塑膜行业发展的关键因素。
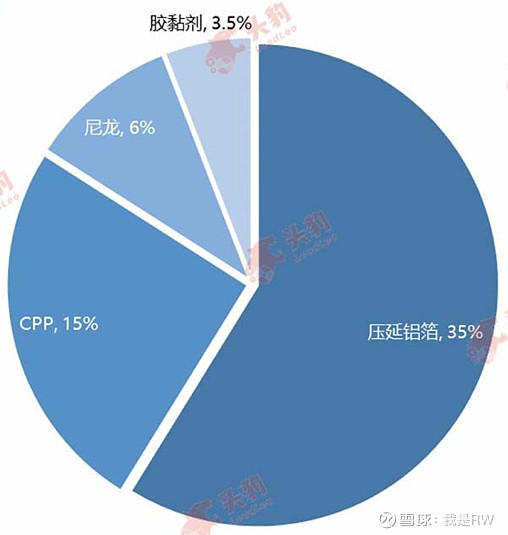
压延铝箔:一种金属铝箔膜,是铝塑膜的核心材料,厚度为 5-9μm,中国压延铝箔生产线领先于日本和韩国,拥有2,000米的辊面生产线,占全球总量的一半。国内领先的压延铝箔企业包括华西铝业、渤海铝业、河南神马等,虽然中国在压延铝箔生产线上占据优势,但在产品性能如耐折度等方面却不及日本等优质企业,主要产品供应在中低端3C消费电子领域。
CPP膜:流延聚丙烯薄膜,主要起到封口粘接的作用,防止电极与电池软包材料之间短路。如果电芯的极耳与CPP膜粘合不牢,会导致电芯出现胀气和漏液的情况,电池就会失效。CPP膜需要有较好的热封粘贴性、耐电解性以及与压延铝箔之间较高的复合强度。中国CPP膜行业起步于20世纪80年代,最初通过引进国外单层流延设备生产CPP膜,现已拥有能够生产宽幅为5.0米的三层流延薄膜生产线,国内企业包括佛塑科技、广东仕诚、佛山俊嘉等都拥有CPP膜生产线,但与国外领先企业相比在自动化程度、技术水平和设备工艺上还有一定差距,生产的产品主要用于3C消费电子中低端铝塑膜。
尼龙层:主要由BOPA膜组成,BOPA膜是双向拉伸尼龙薄膜,在铝塑膜加工过程中能够连续操作不破坏外观,还可防止碰撞对电池造成的冲击,需要具有良好的耐穿刺性、抗冲击性、耐热绝缘性以及耐磨擦性。中国BOPA行业起步较晚,2010年起才有厂家开始生产BOPA产品,国内厂家如沧州明珠、佛塑科技、厦门长塑、运城塑业都已形成了量产,但主要应用领域为3C消费电子铝塑膜,高端铝塑膜用BOPA产品依赖进口。
胶黏剂:在各层之间起到连接作用的“胶水”,需要具有较强的耐电解性、耐温热老化性和粘结性,同时不能与电解液发生化学反应。胶黏剂属于配方型产品,对质量和性能的要求较高,通常由铝塑膜生产企业与胶黏剂生产企业共同研发生产,其工艺配方属于各个企业的商业机密。国内企业在胶黏剂配方生产上还具有一定缺陷,容易导致产品分层剥离的现象,铝塑膜用胶黏剂大部分依赖进口。
总体而言,国产原材料只适应于中低端3C消费电子铝塑膜,而高端3C消费电子铝塑膜和动力软包电池铝塑膜所用的原材料仍然由国外企业提供,高端产品原材料进口依赖程度较高。
1.4.2 中游分析
铝塑膜行业产业链中游参与者主要为铝塑膜生产商。中国铝塑膜行业起步较晚,核心技术缺乏、关键原材料依赖进口,导致中游铝塑膜企业对上游原材料供应商的议价能力较低,尤其对国外原材料进口商的议价能力更低。受益于国内软包电池的迅速发展,国内企业纷纷加速布局毛利润较高的铝塑膜业务,通过自主研发、引进国外生产线、收购外企等方式不断拓展国产铝塑膜行业的市场空间,突破国外铝塑膜企业的技术垄断,同时加强与下游电池厂商的密切合作,通过签订合作协议等方式提高铝塑膜的国产化率,努力实现铝塑膜技术和产能的自主化。
国内铝塑膜企业打开行业市场空间的方式主要由两种:
(1)自主研发方式。以 $明冠新材(SH688560)$ 、紫江企业、 $道明光学(SZ002632)$ 、璞泰来等企业为代表的企业经历了铝塑膜技术从无到有的研发过程,不断解决原材料缺乏、配套工艺设施不完善、测试仪器不全面的一系列问题,打破行业壁垒,生产出耐电解性、剪裁性、隔水性、耐腐蚀性等综合性能较强的铝塑膜,并逐渐实现量产。
(2)收购国外铝塑膜企业。以新纶科技为代表的企业通过收购国外铝塑膜企业迅速布局铝塑膜行业。新纶科技在2016年通过收购日本第三大铝塑膜企业 T&T 的三重工厂,获得其生产铝塑膜的所有设备工艺、专利许可和专有技术使用权,抢占国内铝塑膜市场先机,快速提升了铝塑膜的国产化率,极大促进了铝塑膜行业国产化的进程。自主研发和收购外企两种方式,都促进了中国铝塑膜行业的发展,也在不断挤压日本企业在中国的市场份额,国产铝塑膜正在加速替代进口铝塑膜,中国铝塑膜行业将迎来快速发展。
1.4.3 下游分析
下游需求是促进铝塑膜行业发展的核心动力,中国下游整体需求旺盛,将促进铝塑膜市场规模进一步提升。铝塑膜是软包电池进行封装的关键材料,下游应用领域主要是3C消费电子软包电池、动力软包电池以及储能软包电池。
软包电池的形状设计灵活、能量密度高,符合电子产品小型化、轻薄化的趋势,在3C消费电子领域应用广泛,如智能手机、平板电脑等消费电子产品,苹果、华为、索尼、小米等知名电子品牌目前都采用了软包电池。随着无人机、可穿戴设备等新兴消费电子产品的发展,对电池的轻薄度、容量和安全性要求越来越高,软包电池在3C消费电子领域的渗透率也将保持稳定增长,推动铝塑膜市场需求的进一步增加。
3C消费电子行业逐渐进入成熟期,未来铝塑膜的驱动核心将来自动力软包电池,主要为新能源汽车领域。软包电池安全性能好、重量轻、容量大、内阻小,符合动力电池高能量高密度的发展趋势,是动力电池技术路线的重要选择。全球软包动力电池企业主要为LGC、孚能科技、SKI和AESC。孚能科技为2018年国内动力电池装机量排名前五企业中唯一一家以三元软包动力电池技术起家,且全部为该技术路线产品的企业。当前国内多家方型、圆柱型动力电池企业,纷纷开始布局软包技术路线,建设软包动力电池产能。但软包动力电池行业技术壁垒和工艺制造壁垒较高,要求企业具备相关的研发实力和技术积累,能够进入全球主流整车企业核心供应链的软包动力电池企业较少。
随着中国工业化、信息化水平的不断提升,中国储能市场不断发展,截至2019年底,中国电化学储能市场的累积装机规模达到1709.60MW,同比增长59.4%。在各类电化学储能技术中,锂离子电池的累计装机规模最大,为1378.3MW。2017年,发改委等五部委联合发布《关于促进储能技术与产业发展的指导意见》,首次在国家层面对储能产业进行战略部署。软包电池安全性好、能量密度高,正在向高倍率方向发展,能够更好地满足储能电池的要求。国内已有企业将软包电池应用于储能领域,未来储能领域的发展将提高软包电池的需求,进而促进铝塑膜行业的发展。
2 中国铝塑膜行业驱动因素分析
2.1 行业盈利空间大,进入壁垒降低
铝塑膜行业具有较高的毛利率,率先布局铝塑膜的企业能够迅速抢占市场份额,占领行业的领先地位,对企业未来的发展具有强大的支撑作用,但由于国外领先企业实行技术封锁,国内铝塑膜行业原材料进口依赖程度较高,在缺乏技术和原材料供给的情况下,国内企业进入铝塑膜行业壁垒较高。近些年,原材料供应商逐渐具备了为下游中低端铝塑膜制造商供货的能力,随着国内一批领先企业通过自主研发和收购外企等方式不断拓展国内铝塑膜市场空间,行业进入壁垒逐渐降低,对铝塑膜行业国产化、市场整体水平的提升具有明显的促进作用。
软包电池的成本构成中,占比最高的为正极材料,达到30%。其次是电解液,占比为25%。铝塑膜超过负极和隔膜占比排名第三,为18%,同时铝塑膜是电池原材料中国产化率最低、毛利率最高的一个部分(60%-80%),铝塑膜行业拥有极大的盈利空间。
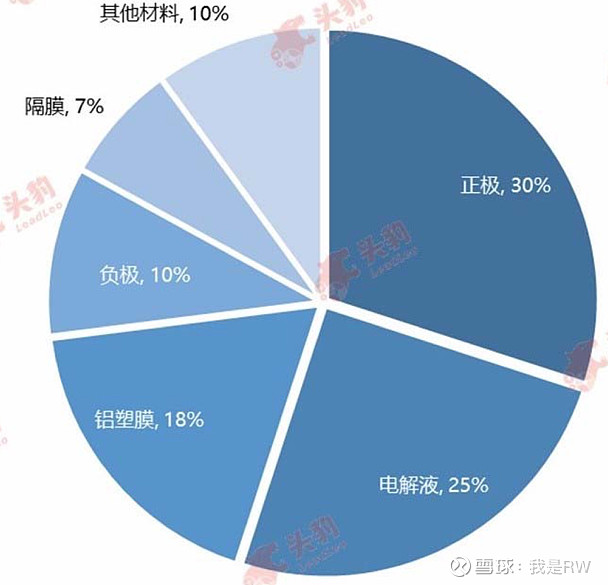
在较高的盈利水平驱动下,国内企业通过提高自主研发能力不断持续布局铝塑膜,既提升了自身竞争实力又推动了行业的发展。紫江企业2004年开始布局铝塑膜,是国内最早依靠自主研发进入铝塑膜行业的企业,现已全面进入中高端3C消费电子类软包电池客户的供应链,产品不断放量替代进口产品。佛塑科技2008年进入铝塑膜行业,产品已外送客户超100家,试用的电池厂商已经入批量电池封装使用阶段。道明光学2014年完成自主研发,2017年进入量产阶段,已与多家电池厂商展开初步合作。新纶科技2016年收购专业从事铝塑膜业务的日本T&T三重工厂,快速布局铝塑膜行业,一跃成为铝塑膜行业的优秀厂商。明冠新材2018年正式量产铝塑膜,且性能达到国际水平,可应用于新能源汽车和储能行业。
国内企业通过布局铝塑膜,盈利能力大幅增加,同时,铝塑膜行业国产化率也从0逐渐提升至10%,促进了行业的快速发展。中国铝塑膜国产化进程已经开启,盈利空间较大及进入壁垒降低将驱使更多企业进入铝塑膜产业链,给行业带来更强大的生命力。
2.2 国产替代需求日渐强烈
中国下游软包电池的迅速发展提高了对铝塑膜产品的需求,但铝塑膜进口依赖程度较高,进口价格居高不下导致下游电池厂商成本压力较大,国产替代的需求日渐强烈,将推动中国铝塑膜行业的景气发展。
2014年至2018年,国内铝塑膜需求量由0.5亿平方米增长至2018年的1.25亿平方米,年复合增长率为 29.1%,预计到2023年,国内铝塑膜需求将在2.94 亿平方米左右,市场需求空间广阔。但国内进口铝塑膜约占总消耗量的90%,进口量巨大。中国铝塑膜行业被日本和韩国的少数企业垄断,国外龙头企业在原材料供应、生产工艺、稳定的下游客户上具有较大的优势,国内企业生产的铝塑膜产品在质量和性能上还不能达到国外优秀企业的标准,无法应用于高端软包电池领域。
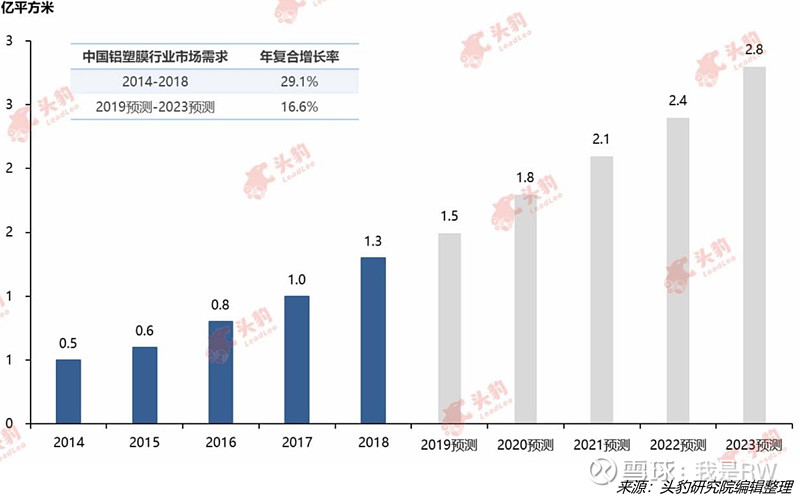
铝塑膜成本占软包电池成本的 15%-20%,进口铝塑膜价格居高不下,给下游电池厂商造成了一定的成本压力。根据2018年财政部等四部委发布的《关于调整完善新能源汽车推广应用财政补贴政策的通知》,新能源汽车需要满足一定的续航里程和技术要求才能获得补贴,且于2019年、2020年补贴出现不同程度的连续退坡。随着新能源汽车行业补贴的下降,成本压力将逐渐转移给产业链中的电池厂商,电池厂商迫切需要降低原材料成本,而在电池的原材料中,铝塑膜国产化程度较低,产品价格水平受制于国外厂商。在铝塑膜需求不断增长、进口价格持续坚挺的背景下,铝塑膜实现国产化的呼声越来越高,市场空间广阔。
若铝塑膜能够实现国产化,巨大的市场需求将推动铝塑膜行业的飞速发展,拉动国内铝塑膜企业的市场份额不断提升,提高国内企业竞争力和市场地位。
2.3 软包电池发展潜力巨大
铝塑膜下游主要应用领域包括3C消费电子软包电池、动力软包电池和储能软包电池。软包电池首先应用在3C消费电子领域,随着在3C消费电子领域的渗透率不断提高,软包电池行业得到了快速发展。同时,新能源汽车行业的快速发展,使得动力领域的需求增长成为软包电池行业的重要驱动力。储能领域是软包电池应用的新兴领域,短期市场需求较低,但国家积极鼓励支持发展储能电池,推动实现储能电池向规模化发展转变,在政策的支持下,储能电池有望实现快速增长,软包电池安全性好、能量密度高,正在向高倍率方向发展,能够更好地满足储能电池的要求,未来储能软包电池具有较大的增长潜力。
(1)3C软包电池
3C软包电池是铝塑膜应用最广的领域。
软包电池体积小、重量轻的特点符合电子产品智能化、轻量化、小型化的发展趋势,在智能手机、平板电脑等消费电子产品中被广泛应用。受益于3C消费电子市场的日渐成熟,软包电池在3C消费电子市场的渗透率保持稳定增长, 而可穿戴设备、无人机等新兴消费电子产品的兴起,为3C软包电池提供了新的发展动力。整体而言,3C软包电池对铝塑膜的需求较大,未来将保持稳健的增长速度。
(2)动力软包电池
动力软包电池是未来铝塑膜的重要应用领域。
未来全球新能源汽车市场的增长主要由新能源乘用车拉动,其对动力电池系统的能量密度、安全性能要求更高。由于软包动力电池拥有能量密度高、安全性能优异、循环寿命长的特点,越来越多国内外车企开始选择软包动力电池。未来,软包动力电池渗透率有望不断提升。
以往国内新能源汽车动力电池在使用上偏向于圆柱形与方形电池,但新能源汽车对动力电池能量密度及安全性的要求越来越高,软包电池越来越受到国内车企的重视。随着新能源汽车补贴政策和能量密度以及电池续航能力挂钩,将会有更多的车企选择软包动力电池,软包动力电池在新能源汽车领域的渗透率将大幅度提升。新能源汽车行业的快速发展,也将带动软包锂电池的需求量快速增加。用车领域,主流车企纷纷开始选择软包动力电池。LGC、AESC、SKI均为日韩软包动力电池企业代表,已为大众、奥迪、日产、现代起亚、通用、雷诺等车企配置了多款主流车型。近年来,国内如东风、众泰、北汽新能源、比亚迪等主流电动车企也纷纷开始尝试软包动力电池,主要供应商有ATL、多氟多、微宏动力、中航锂电等,近期上海卡耐新能源、山东恒宇、苏州宇量等很多企业也开始大力投建软包动力电池生产线。
自2012年国务院发布实施《节能与新能源汽车产业发展规划(2012-2020年)》以来,我国新能源汽车呈现快速发展态势,产销量逐年迅速增长。2019年,受补贴退坡影响,叠加二手新能源车的低价冲击,我国新能源汽车产销量出现首次下降,但中长期来看,随着退坡政策影响的边际减弱及国家对新能源汽车鼓励政策的退出,新能源汽车产业向好趋势不变。2020年底我国新能源汽车产业发展工信沙龙称未来中国新能源汽车产销量有望继续上升,预计2021年增幅将超过30%,产销达180万辆。动力软包电池需求将大幅增长,将推动铝塑膜需求的大幅攀升。
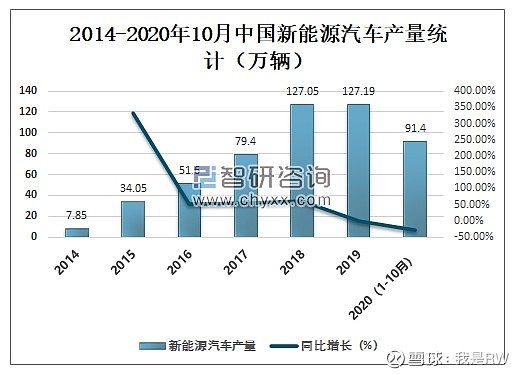
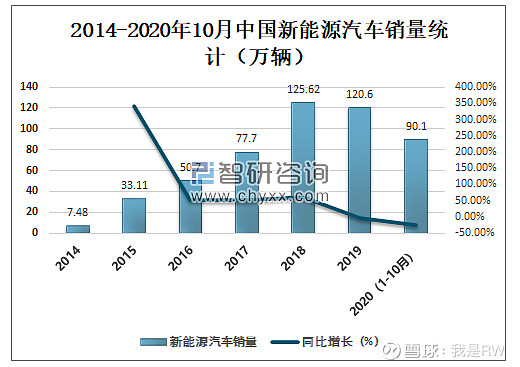
(3)储能软包电池
虽然中国储能行业起步较晚,市场需求没有实现大规模爆发,但储能电池具有环境污染低、能量密度大、工作温度范围宽、可快速充放电、使用寿命长等优点,在近些年得到广泛应用,具有良好的市场发展潜力。软包电池正逐渐向高倍率应用的方向发展,可更好地满足储能电池的要求,在储能领域拥有巨大的市场空间。2017年10月,发改委等五部委联合发布《关于促进我国储能技术与产业发展的指导意见》,鼓励积极发展储能电池,实现储能电池向规模化发展转变,在政策支持下,未来储能电池将保持较高增速,不断拉动相关铝塑膜需求上升。
基于3C软包电池稳定增长、新能源汽车动力软包电池市场前景广阔以及储能软包电池良好的增长潜力,铝塑膜下游市场整体需求强劲,将对中游铝塑膜行业起到明显的促进作用。
3 中国铝塑膜行业制约因素分析
3.1 原材料高度依赖进口
由于国内原材料生产还达不到较高标准,不能满足部分铝塑膜厂商对原材料的需求,所以部分中低端铝塑膜和全部高端铝塑膜所需原材料都依赖进口,是制约铝塑膜行业发展的瓶颈之一。铝塑膜生产所需的原材料主要是压延铝箔、CPP、尼龙和胶黏剂,中国原材料供应商由于缺乏技术积累,生产的铝塑膜产品质量和性能较进口产品存在一定差距,只能应用于中低端铝塑膜,而高端铝塑膜所需原材料依赖高度进口。
由于原材料高度依赖进口,铝塑膜厂商在产业链中处于被动地位。中国铝塑膜行业还处于初步发展时期,没有形成较规范的市场竞争格局,部分企业暂时处于试产试销阶段,国内企业通常与下游电池制造商签订合作协议来进行产品生产,而铝塑膜的生产和经营情况较大程度受制于上游原材料供应商:
(1)若原材料供应商发生产量不足、经营状况恶化等情况,中国铝塑膜企业可能在短时间内无法及时获取充足的原材料供应,产品出货量将会受到影响,进而影响对下游电池厂商铝塑膜的供应,拉长供应周期,不利于产品的推广和市场份额的扩大。
(2)若与原材料供应商出现合作中断的情况,铝塑膜厂商需要重新寻找原材料供应商,会消耗时间、金钱和精力造成原材料成本的增加,从而削弱铝塑膜厂商的盈利能力。
3.2 核心技术积累不足
铝塑膜国产化率较低主要是因为行业壁垒较高,国内的产品性能很难达到日本企业的水平,在原材料处理技术、胶黏剂配方技术和设备工艺方面存在较大差距。虽然中国铝塑膜企业通过不断进行自主研发新工艺,生产的铝塑膜产品获得了国内下游电池厂商的认可,但国产铝塑膜主要应用于中低端软包电池市场,高端铝塑膜仍然依赖进口。在原材料处理工艺上,国内技术仍存在一些问题。例如:
(1)铝箔表面处理工艺落后、污染大。
铝箔的水处理会出现“氢脆”,导致铝塑膜耐拆度差。铝箔表面挺度不够,良品率差。聚丙烯与高导热的铝箔表面复合时易卷曲,出现层状结晶。国内胶粘剂配方工艺较差,易出现分层剥离问题。
3.3 信心积累不够
中国铝塑膜行业起步晚于日本、韩国等发达国家,2015年起国内铝塑膜产品才开始陆续投产,发展历史较短。下游动力电池厂商为了保证产品的质量,通常要求铝塑膜产品具有三到五年的安全使用认证期,大多国产铝塑膜还不能满足这个要求。信心的建立需要一定的时间,市场持续供货,产品应用稳定,供货时间越长,市场认可度越高,才会迎来爆发期。
整体而言,中国铝塑膜市场被日本、韩国企业所垄断,国内企业市场占有率约为 10%,进口铝塑膜价格持续居高不下,国产铝塑膜企业在核心技术上的缺失将限制行业的发展速度,中国铝塑膜全面实现国产化任重道远。
4 中国铝塑膜行业政策及监管分析
4.1 中国铝塑膜行业支持政策分析
近几年,中国政府颁布了一系列政策鼓励支持动力电池产业的发展,为动力电池行业提供了方向指导和动力支持。铝塑膜作为软包动力电池封装的关键材料,受到政策支持的影响较为明显。
2016年12月,国务院发布《“十三五”国家战略性新兴产业发展规划》,提出到2020年,力争使若干新材料品种进入全球供应链,重大关键材料自给率达到70%以上,初步实现从材料大国向材料强国的战略性转变。在动力电池产业链中,只有铝塑膜还没有实现国产化,进口依赖度较高,若能够尽快实现铝塑膜国产化,中国将实现动力电池产业链全布局,该发展规划的颁布,可起到推动铝塑膜行业国产化进程的作用,为铝塑膜行业的发展提供动力支持。2017年2月,中国工信部等四部委发布《促进汽车动力电池产业发展行动方案》,到2020 年,新型锂离子动力电池单体比能量超过300Wh/kg,系统比能量力争达到260Wh/kg,到2025 年,新体系动力电池技术取得突破性进展,单体比能量达 500Wh/kg。2017年4月,中国工信部等三部委发布《汽车产业中长期发展规划》,提出到2020年新能源汽车年产销达到200 万辆,动力电池单体比能量要求达到300Wh/kg,力争实现350Wh/kg,系统比能量力争达到 260Wh/kg。目前还没有达到政策要求,而使用软包电池可以使系统能量密度提升 5%-15%,中国政府对动力电池高能量高密度的要求能够促进软包动力电池渗透率的不断提升,进而促进铝塑膜行业的快速发展。2019年财政部等四部委发布《关于进一步完善新能源汽车推广应用财政补贴政策的通知》,将新能源乘用车的系统能量密度与续航里程作为国家补贴政策的重要考核指标,规定纯电动乘用车动力电池系统的质量能量密度不低于 125Wh/kg,125(含)-140Wh/kg的车型按0.8倍补贴,140(含)-160Wh/kg的车型按0.9倍补贴,160Wh/kg及以上的车型按1倍补贴。该补贴政策的实施对新能源汽车动力电池的性能提出了更高的要求,软包动力电池符合动力电池高能量高密度的发展趋势,将提高软包动力电池的需求,进而推动铝塑膜行业的快速发展。2016-2020年继续实施新能源汽车推广应用补助政策,并且2016-2020年各项补贴在2015年的基础上保持一定速度的退坡。
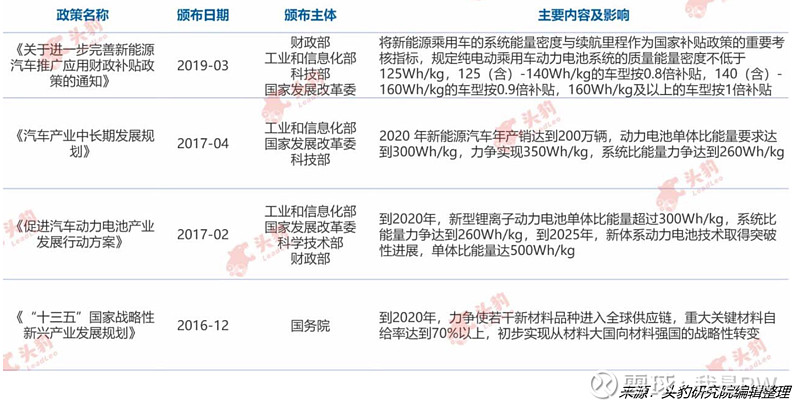
4.2 中国铝塑膜行业监管政策分析
由于缺乏铝塑膜行业的国家标准和行业标准,各电池生产企业、铝塑膜生产厂家的技术性能要求和测试方法差异较大,产品品质良莠不齐,同时缺乏权威的相关测试机构,从而严重阻碍了行业的发展和进步。2018年12月,中国化学与物理电源行业协会颁布了中国第一部《锂离子电池用铝塑复合膜》团体标准,标准于2019年1月1日开始实施,规定了锂离子电池用铝塑膜的术语和定义、分类、要求、试验方法、检验规则及标志、包装、运输和贮存。该标准的实施有助于加强铝塑膜行业的管理,营造良好的市场竞争环境,推动铝塑膜行业健康有序发展。

5 中国铝塑膜行业发展趋势分析
5.1 国产替代进程加快
中国软包电池厂商使用的铝塑膜大部分依赖进口,进口铝塑膜成本高,给下游电池厂商造成了一定的压力,同时不利于国内铝塑膜行业的发展。国内铝塑膜在质量和性能上与国外高端产品存在一定差距,主要供应中低端3C消费电子领域,还不能满足高端市场的要求。随着中国铝塑膜持续放量、技术工艺和设备不断完善,铝塑膜在一致性和耐电解性等关键性能上都有了一定的提升,国产替代的进程将逐渐加快。
对比进口铝塑膜,国产铝塑膜有以下优势:
(1)价格优势。国产铝塑膜在价格上较进口铝塑膜低20%-30%,下游电池厂商进口依赖程度高,议价能力弱,对铝塑膜价格敏感。此外,进口铝塑膜年度降价幅度为2%-3%,国产铝塑膜产品年度降价幅度为7%-9%,进口产品价格居高不下,在同等情况下,国内电池厂商更倾向于选择国产铝塑膜产品。
(2)服务优势。国内铝塑膜企业在向下游电池厂商供货时,可保障配送及时、货源充足,能够提供完善的售后服务,在不良率的处理上面会更加迅速和完善,技术服务更全面、便捷。
(3)销售策略灵活。国内铝塑膜企业市场开拓渠道更加直接,销售策略更灵活、交易方式更方便。
国内铝塑膜产品具有较强的性价比优势,已经逐渐打开了3C消费软包电池和软包动力电池的市场。国产中低端铝塑膜在质量和性能上能够达到下游厂商的标准,软包电池领军企业ATL、珠光宇等公司已经开始批量应用国产3C消费电子类铝塑膜,同时国内一些电池企业也开始对国产铝塑膜进行测试和调试,若能通过验证,则会大力提高国产铝塑膜的出货量。随着技术进步和国内企业布局的加速,中国铝塑膜行业国产化率将逐渐提高。
5.2 疫情后期需求重心落在3C,从长期看需求重心向动力市场转移
现阶段国产铝塑膜在储能领域及新能源汽车领域受到较大影响,消费电子3C领域增量趋势明显。随着国际疫情发展,国外供应链渠道受阻进一步加剧,软包锂电厂家应加强国内供应链厂家的试样与开发进度,特别是对全面国产化体系的铝塑膜开辟绿色通道,帮助供应链国产化提升。
从长远来看,锂电行业发展及技术发展路线没有改变,因此后疫情时代更应保持战略定力。3C消费电子行业逐渐进入成熟期,未来铝塑膜驱动核心力来自动力软包。同时,随着新能源行业的逐渐火爆,需求增加,软包电池新能安全性能好,能量密度高,可满足新能源汽车动力电池高能量密度和高续航里程要求,势必成为未来动力电池主流发展,未来铝塑膜的需求重心将由3C消费电子市场向动力市场转移。
5.3 进军高端产品
随着铝塑膜需求的日益增加,国内企业也加快了布局铝塑膜行业的步伐,在实现了中低端铝塑膜产品批量供货之后,国内企业开始发力进军高端铝塑膜领域。国产铝塑膜存在性价比优势,但产品性能和质量离国外高端铝塑膜还存在一些差距,不能满足下游高端电池领域的要求。随着下游动力电池的不断发展,对高端铝塑膜的需求将逐渐增加,高端铝塑膜全部依赖进口既不利于国内铝塑膜厂商自身的发展,也在一定程度上阻碍了铝塑膜国产化的进程。
近年来,国内企业通过技术研发、收购外企、引进生产线等措施,不断对工艺技术以及生产设备进行完善更新,其产品质量和性能有了进一步的提升。国内已有部分企业逐渐布局高端动力电池用铝塑膜,并开始送样检测,国内电池厂商也已经开始对国内高端铝塑膜产品进行测试等工作,如明冠新材已送样 $宁德时代(SZ300750)$ 进行测试验证。
由于动力电池企业在选择国产铝塑膜替代产品时更为谨慎,测试器和试用期较长,如果国产高端铝塑膜产品通过认证并开始供货,则国产铝塑膜行业将实现快速增长。国产铝塑膜需要面对的应用技术问题提升及管理提升的需求正在迅速被提高,自身完善的现状没有根本改变,但都在加速做好稳定产品与应用性提升的工作,逐渐缩小差距。在明冠新材、紫江企业、道明光学等一批具有竞争实力的企业共同带领下,随着技术水平的进一步提高,国内企业在高端铝塑膜市场的占有率将进一步提升。
6 中国铝塑膜行业市场竞争格局
6.1 中国铝塑膜行业竞争现状分析
中国铝塑膜行业起步较晚,还没有形成稳定的竞争格局,市场基本被日本企业所垄断。在中国铝塑膜市场上,日本DNP和日本昭和电工占垄断地位,处于第一梯队,市场份额占比为 70%,新纶科技于2016年收购日本T&T铝塑膜业务的三重工厂,凭借技术积累和销售网络,成功迈入铝塑膜市场第一梯队。韩国栗村化学、日本大仓工业、日本东冈工业位于中国铝塑膜市场的第二梯队。明冠新材、道明光学、东莞卓越、紫江企业位于中国铝塑膜市场的第三梯队,中国铝塑膜国产化率约为 10%。
中国铝塑膜产品主要面向 3C 消费电子领域,与国际化标准还存在一定差距,不能满足中高端市场需求,但中国铝塑膜企业通过自主研发新工艺和新设备,在技术工艺、材料设备等方面不断突破行业壁垒,生产的铝塑膜产品在质量和性能方面都有了很大的提升,已有部分企业开始布局动力电池用铝塑膜。中国铝塑膜企业通过研发新技术、引进进口生产线、并购外企等多种途径不断拓展市场空间,在明冠新材、新纶科技等具有竞争实力的企业带动下,国产铝塑膜企业将通过成本优势逐步提高市场占有率。
6.2 中国铝塑膜行业的主要参与者
6.2.1明冠新材(688560)
6.2.1.1公司简介:公司铝塑膜项目成立于2010年,明冠新材主要经营太阳能电池背板、铝塑膜、特种防护材料等新型复合膜材料,是一家专注新能源及建材交通领域先进新型材料研发和制造的国家高新技术企业。公司拥有自主知识产权的发明专利等各类专利90余项,服务客户包括国电投、中节能、LG、REC、韩华、比亚迪等。2020年12月24日,明冠新材料股份有限公司正式在上交所科创板挂牌交易。
6.2.1.2公司业务及核心优势:目前明冠新材料铝塑膜研发人员超过30人,获得铝塑膜专利30+项。公司的铝塑膜业务2010年开始立项,从2016年起送样评测,目前均得到合格通过,2018年铝塑膜实现量产,目前铝塑膜产能为300万平米。
明冠新材铝塑膜产品采用干热复合法,优势在于吸取干法工艺优势的同时,兼顾了热法在耐电解液和抗水性方面具有优势的工艺特点,使得铝塑漠在冲深成型、外观、裁切性能、耐电解液及阻水性能方面的综合性能得到了全面提升。明冠新材铝塑膜产品具有优良的冲壳成型性、优异的耐腐蚀性能、优越的绝缘性能。前国内大多数的铝塑膜厂家一般冲坑在6mm左右,国外日本的冲深在8-12mm,而明冠锂膜的干热法产品正常生产的冲深在9-10mm,对比国内外产品性能,明冠新材铝塑膜研发的产品性能接近日本,高于国内,可在纯电动力汽车的动力电池上安全运用。公司已于动力电池龙头宁德时代建立业务联系,铝塑膜样品正在宁德时代的测试验证中。
6.2.1.3:2017年-2019年及2020年上半年,铝塑膜产品收入占公司主营业务收入的比例分别为0.01%、0.80%、5.89%和9.06%,虽然锂电池用铝塑膜产品销售收入占公司总量并不大,但近几年的发展非常迅速,年增速超100%。公司远期规划铝塑膜产能达1亿平方米,将再造3个明冠。
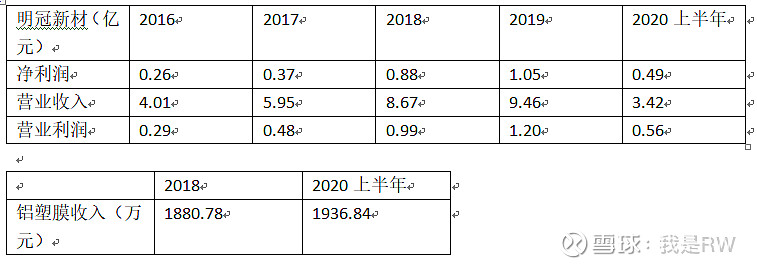
6.2.2道明光学(002632)
6.2.2.1公司简介:道明光学股份有限公司是专业从事研究、开发、生产和销售各种反光材料及反光制品的国家级高新技术企业,建有省级高新技术研究开发中心及省级企业技术中心,拥有三十多项自主知识产权,产品质量达到国际领先水平。2011年11月22日在深圳证券交易所中小板挂牌上市。
6.2.2.2公司业务及核心优势:目前道明光学股份有限公司的主营业务根据应用场景及领域的不同细分为个人安全防护材料及制品、车辆安全防护材料及制品、玻璃微珠型道路安全防护材料及制品、微纳米棱镜型反光材料及制品、液晶显示用背光材料及模切组件、锂离子电池封装用材料、光电薄膜/板材、高性能离型材料等几大板块。公司铝塑膜采用干法工艺,具有优良的外观和剪裁性能,冲压成型性,耐解液腐蚀性和优越的热封强度及极耳胶适配度。已于2017年二季度已经进入稳定的量产阶段,各项性能指标与国外品牌同类产品性能较一致,各项性能指标都达到或超过了行业内公认的技术性能要求。已获得超过50家3C锂电池企业订单,主流动力客户均处于认证阶段,有部分小厂家及助动车、储能车客户已采购使用动力类膜,2019年公司加大动力类用铝塑膜的销售,塑膜产能为1,500万平方米。
6.2.2.3:
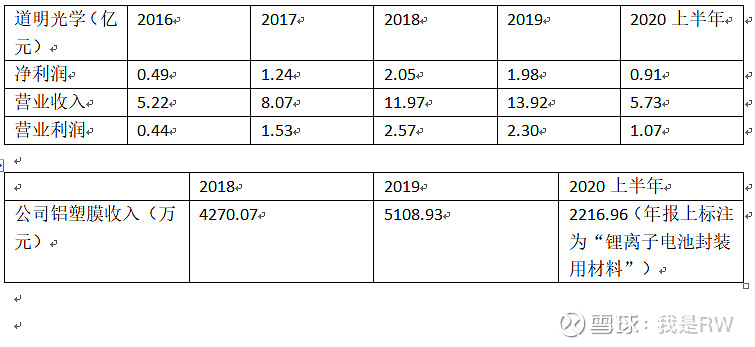
6.2.3新纶科技(002341)
6.2.3.1 公司简介:深圳市新纶科技股份有限公司创立于2002年,2010年在深交所上市。2016年,新纶科技斥资95亿日元(彼时按汇率约合人民币5.5亿元)收购了日本T&T的铝塑膜业务。收购完成以后,新纶科技获得T&T在日本三重县的锂电池铝塑膜工厂及相关资产,并获得制造及销售铝塑膜软包产品的全部专利和专有技术在中国的独占许可及在日本的非独占许可。新纶科技收购T&T铝塑膜业务之后,其铝塑膜业务尤其是动力领域面临多重挑战。随着市场竞争加剧和补贴进一步退坡,加上日本DNP和昭和电工在国内市场的激烈竞争,新纶科技的铝塑膜业务也遭遇巨大的压力和挑战。产品价格下滑和原材采购成本上升导致其铝塑膜盈利能力出现下滑。2020年4月9日,新纶科技收到证监会下发的《行政处罚实现告知书》,披露新纶科技存在通过虚构贸易业务虚增2017和2018年度收入及利润、未按规定披露2017- 2018年期间关联交易、未按规定披露2017年对外担保等问题。此外,公司经营业绩大幅下滑,2019 年归属上市股东的净利润大幅减少,2020 年一季度出现亏损。2020年10月20日,新纶科技选择剥离其铝塑膜业务交由其子公司独立运营,并出售子公司超过50%的股权,短期可缓解其资金压力。但由于其子公司当前处于亏损状态,或将给其铝塑膜业务在未来融资扩产方面产生压力和挑战。公司因财务造假最近几年无法增发、中短期财务压力巨大,逾期银行欠款不少,大股东股票接近全部质押,财务与资金扑朔迷离。
6.2.3.2公司业务及核心优势:目前公司形成了电子功能材料、新能源材料、洁净室产品与净化工程三大核心产业,构筑起电子功能材料、锂电池软包材料、超净产品与清洗、净化工程、精密模具、医护产品等业务集群。拥有深圳、苏州、常州、天津、上海、成都六大产业基地,分支机构遍布国内主要城市、港台地区和美国、德国、日本、东南亚等国家,下属30多家控股子公司。新纶科技主要采用干法工艺制备铝塑膜,产品类型以86、113、152μm为主。
6.2.3.3:
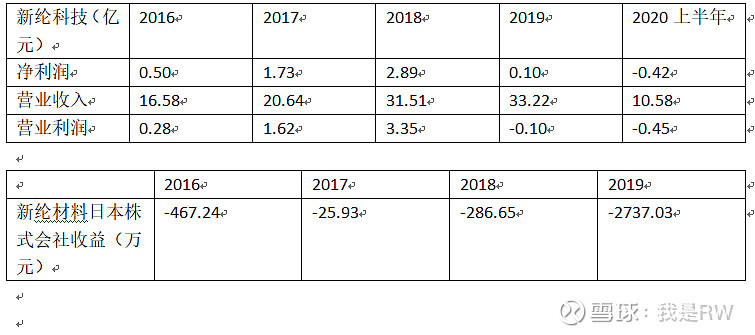
6.2.4璞泰来(603659)
6.2.4.1 公司简介:上海璞泰来新能源科技股份有限公司于2012年成立,2017年上市。公司为下游客户提供专业性、高品质的新能源锂离子电池材料及专业工艺设备综合解决方案,通过渠道共享、研发合作、工艺配套等实现了关键业务价值链的产业协同。
公司主要产品为负极材料、涂布机、涂覆隔膜、软包电池用包装膜、纳米氧化铝粉。
6.2.4.2公司业务及核心优势:公司经营范围包括高性能膜材料、锂离子电池、电池材料及专用设备技术领域内的技术开发等。公司长期致力于研究锂离子电池铝塑包装膜的特种CPP材料、尼龙表面耐电解液涂层、环保型铝箔处理工艺、热复合及热处理工艺等一系列的关键技术,解决了PP铝层间粘结力、尼龙耐腐蚀性、电芯边电压性能、极限冲坑深度、PET与PA粘接性等一系列产品特性难题,产品性能接近进口铝塑膜水平,基本实现了原材料和工艺设备的全面国产化替代。
2020年上半年,公司铝塑包装膜产品实现出货量253万平米,同比持平。公司铝塑包装膜已在数码产品如充电宝、手持吸尘器等领域实现批量供应;与此同时,公司不断加快铝塑包装膜产品的推广渗透,在笔记本电脑、电动自行车等产品应用和批量供应。随着溧阳卓越制造工艺及产能的逐步完善,公司将积极进军高端消费及动力软包市场,出货量可望得到明显改善。
6.2.4.3 :
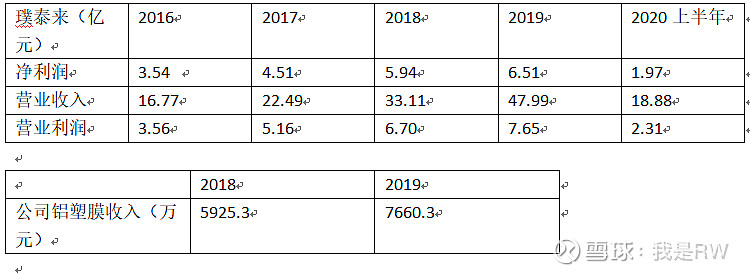
6.2.5紫江新材料(未上市)
6.2.5.1 公司简介:上海紫江新材料科技股份有限公司为上交所上市公司紫江企业的控股子公司,2011年由紫江企业(沪市代码600210)与新上海国际组件成立,拟将分拆至科创板上市。
6.2.5.2公司业务及核心优势:公司主要从事锂电池包装铝塑膜的研发、生产和销售。紫江新材料占地面积10万平方米,建筑面积18000多平方米,具备10万级洁净车间1万多平方米,拥有复合、涂布和分切等具有国际领先水平的生产线。公司主要采用干法工艺制备铝塑膜,产品类型以88、113、123、152μm为主。公司产品覆盖从低端到高端的全系列产品,在3C数码领域已经批量供应ATL、光宇、力神等企业,在动力领域,产品主要应用于物流车、电动自行车。公司在3C数码市场保持稳定放量的优势,同时大力开拓动力铝塑膜市场,增加了电动自行车用铝塑膜的销售。目前月产能达到300万平方米
6.2.5.3
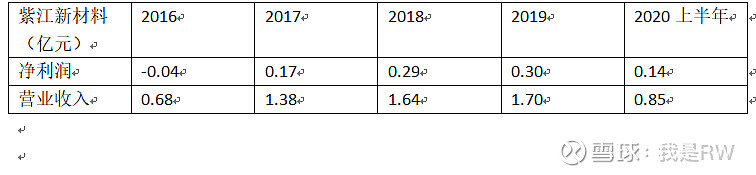
6.2.6苏州锂盾(未上市)
6.2.6.1公司简介:苏州锂盾是中国华融资产与湖北高投旗下投资的企业,于2015年6月注册成立。
6.2.6.2公司业务及核心优势:目前,公司铝塑膜已形成三大系列九个产品,具有优异的深冲性能、电气安全性能和长期高阻隔耐腐蚀性能,为汽车动力电池、储能电池、高端消费电子电池,高倍率电池、聚合物电池、固态电池等提供高能、安全的封装差异化解决方案。
苏州锂盾全球首创发明的Microlayer TM非极性微波锚固法多相界面一体化铝塑膜工艺专利技术,突破了日韩企业铝塑膜装备、技术封锁,填补了中国高端铝塑膜研发产业化技术的空白。该技术整个环节都是独立研发,并已实现完全国产化,在制造运维环节及成本管控环节都有着较大优势,可以充分发挥锂电池软包系统寿命安全、成本降低、能量密度提升上的优势,帮助锂电池软包实现全面“中国芯”。
在技术优势上,苏州锂盾单坑极限深冲可达10mm,2019年底实现14mm,2020年实现双坑40mm,高温电解液长期耐腐蚀可达2000h,关键产品指标具备行业领先水平。目前,苏州锂盾已申请国家专利55项,授权32项,核心专利拥有量行业领先,并先后与西安科技大学、东南大学、中南大学、中化国际、中铝集团等高等学府和央企签订了战略合作协议。是目前国内唯一承担“十三五”重点研发计划大容量高功率密度锂电池铝塑膜关键技术研发与产业化项目的企业。
公司产品主要用于3C数码类,已有小批量出货并获得专利,未来两年投入1亿元建设2000万平方米动力电池铝塑膜产能和研发中心,年产值达6亿元